What is Wool Fiber?
Wool fiber is a lasting natural fiber that nature has given us and has been cherished by people for its warmth and long-lasting quality for generations. It is a textile fiber that is obtained from animals like sheep, goats (providing cashmere and mohair), muskoxen (for qiviut), rabbits (for angora), and camelids, each offering different types of wool.
History of Wool Fiber
Archaeological findings point to the beginnings of sheep domestication in ancient Mesopotamia between 11,000 and 8,000 BCE. These early sheep, descendants of wild mouflon, served primarily for meat, hides, and milk. Notably, small statues from Iran depicting woolly sheep date back to approximately 6000 BCE, indicating the early stages of Persians breeding sheep for wool. The earliest known woolen clothing can be traced to 4000-3000 BCE.
Sheep were introduced to Europe through Egypt and the region around modern Marseille, France, around 6000 BCE. By 1000 BCE, England and Spain had become Europe’s primary wool producers. Sheep played vital roles in Greek and Roman cultures, with evidence of a substantial Roman wool processing facility in Winchester, England, dating to around 50 CE.
The introduction of fine-wooled sheep to Europe, particularly the Merino breed, occurred after the importation of ancestors from Morocco to Spain. In the Americas, sheep were brought by Christopher Columbus in 1493 and Hernán Cortés in Mexico in 1519. These early shipments brought Churras sheep to the Navajo people in the late 1500s, laying the foundation for the modern Navajo-Churro sheep breed.
Although sheep were brought to Virginia in 1607, they were consumed during a famine. However, in 1609, sheep were successfully reintroduced, and by the 1640s, there were over 100,000 sheep in the thirteen British colonies. As settlers moved westward in the 1800s, sheep populations expanded. By the 1940s, the United States had over 55 million sheep. Nevertheless, these numbers have declined, with fewer than 5 million sheep in the United States today.
Today, China and Australia lead the world in wool production. Sheep arrived in China and Mongolia around 3000-2000 BCE, with China producing over 386 metric tons of wool annually. Australia, known for high-quality Merino wool, yields over 382 metric tons per year.
Wool’s reputation is well-deserved due to its unique molecular structure. Each wool fiber resembles a tiny spring, offering impressive stretch and resilience. When wet, wool fibers can be stretched up to 50% of their length, and up to 30% when dry, returning to their original state upon release. Wool’s inherent flexibility results in remarkable durability, as a single wool fiber can withstand over 20,000 bends without breaking, in stark contrast to cotton, which breaks after approximately 3,000 bends.
Properties of wool fiber
The microscopic view reveals the unique characteristics of wool. Its surface consists of overlapping protein scales, all pointing toward the tip. In animals, this structure allows foreign matter to gradually escape from the fleece. In yarn, it enables the fibers to interlock with one another, which is the secret to wool’s strength.
Wool’s surface acts as a natural water repellent. Since moisture doesn’t linger on the surface, wool fabrics typically feel dry and comfortable even in damp conditions. However, the inner core can absorb moisture. Surprisingly, wool can absorb nearly twice its weight in water while still feeling relatively dry. This absorbent property also contributes to wool’s resistance to wrinkles and helps prevent the buildup of static electricity. Additionally, due to its inner moisture content, wool inherently possesses flame resistance.
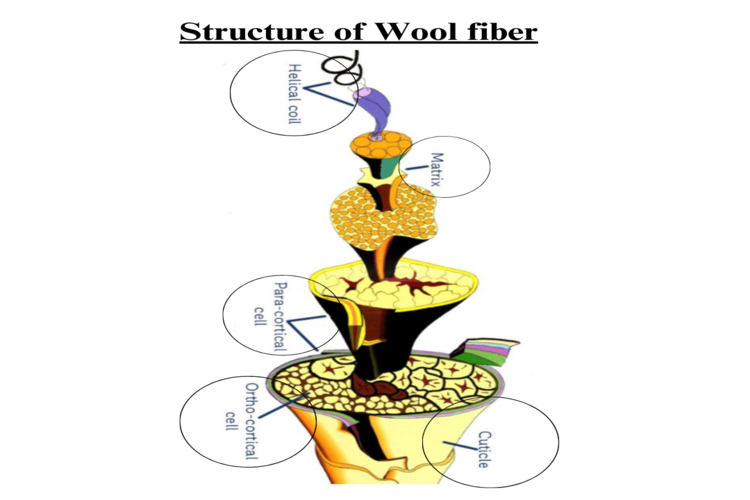
Structure of Wool fiber
Wool fiber has a complex physical structure. Its surface consists of overlapping cuticles, creating a textured, scaly appearance that’s quite different from the smooth surface of synthetic fibers. These scales serve as a protective barrier against dirt and are essential for the felting process. Lanolin, a waxy substance produced by glands surrounding the cuticle, acts as a protective shield for sheep, keeping them safe from the elements and repelling water while allowing the absorption of water vapor. During wool processing, lanolin is extracted and sold as a by-product of the wool production process.
The interior of wool is intricate and comprises various components, including the membrane, cortex, cortical cell, microfibril, matrix, and microfibril, as well as a twisted molecular chain and helical coil.
Membrane: This fiber component allows dyes and moisture to penetrate, enabling the fiber to absorb humidity.
Cortex: Comprising 90% of the fiber, it’s formed by millions of cells that combine to create cortical cells.
Cortical cells: In fine wool, there are two main types, para-cortical and ortho-cortical, each with a unique chemical composition responsible for giving wool its crimp.
Microfibrils: These are long filaments found inside the cortical cells, made up of microfibrils.
Matrix: It’s responsible for granting wool its absorbent, fire-resistant, and anti-static qualities. The high sulfur proteins in the matrix attract water molecules, allowing wool to absorb up to 30% of its weight in water.
Twisted molecular chain and helical coil: These protein chains act like springs, providing wool with flexibility, elasticity, and resilience to maintain its shape without wrinkles.
Chemical Composition of Wool
- Keratin 33%
- Saint 28%
- Fat 12%
- Mineral matter 1%
- Different impurities 26%
Processing of Wool fiber
Wool fibers undergo several manufacturing steps to create the woolen fabric used in various apparel and clothing items. In the following sections, I’ll guide you through the steps of processing wool fibers.
1. Shearing: Every year, sheep are sheared to gather wool fibers. Expert shearers, who handle multiple sheep each day, perform this task. The average fleece from a sheep weighs about 6 to 18 pounds. While most sheep are sheared by hand, modern technology allows for more comfortable shearing using computer-controlled arms and robots.
2. Grading and Sorting: Fleece is graded based on its quality and sorted into different sections depending on its quality and the part of the body it comes from. The finest wool fibers are obtained from the sheep’s shoulder and sides, while the lowest-quality fibers are taken from the lower leg.
3. Scouring: Wool contains a greasy substance, primarily lanolin, dirt, suit, and sand, which needs to be removed to obtain pure wool fibers. This process, called scouring, involves passing the greasy wool through bowls filled with warm water, detergent, and alkali to eliminate impurities. The wool is then rinsed in fresh water, and mechanically dried, and any remaining sand or impurities are removed. Afterward, the wool fibers are blended and conditioned.
4. Carbonizing: Carbonizing is done to remove vegetable matter like seeds, burs, and grass from the wool. These vegetable impurities can be dissolved easily by using a strong solution of sulfuric acid, followed by baking in a dryer. The wool fibers are then passed through a dryer at temperatures ranging from 95 to 120 degrees Celsius. Subsequently, they go through fluted rollers to crush carbonized burs and remove any dust using a de-dusting roller.
5. Neutralization: The sulfuric acid left in the wool fibers after carbonization is removed through a neutralization process. The fibers are rinsed in cold water and then passed through a soda bath at 37 degrees Celsius, followed by an ionic wash. Neutralization takes approximately 12 minutes at a pH of about 6.5, after which the fibers are dried.
6. Carding: The wool fibers are separated and blended into slivers by passing them through metal teeth. This process, known as carding, also removes any residual dirt particles and opens the fibers into individual strands. Carding can be done using hand carders or drum carders, resulting in a uniform sheet of fibers with consistent thickness known as a sliver.
7. Backwashing: After carding, an additional scouring treatment is performed on the wool slivers to remove any dirt or impurities picked up during the carding process. This step is referred to as backwashing.
8. Gilling and Combing: Gilling is the process of aligning wool fibers so that they can lie parallel to each other. Combing is generally performed to eliminate the short fibers in the wool. Both processes straighten and refine the sliver, reducing its weight per unit length.
9. Drawing: Fiber tops are drawn to blend them thoroughly, ensuring evenness and regularity in the roving material. The tops are passed through rollers to reach a specific thickness, with a slight twist added to increase their strength.
10. Spinning: Wool fibers are spun together to form a single strand of yarn. The natural clinging and sticking properties of the fibers make spinning wool yarn a straightforward process. Woolen yarn is typically mule-spun, while worsted yarns are produced using various spinning machines. The resulting yarn is wound around bobbins, cones, or drums.
11. Steaming: Steaming is carried out to set the twist and prevent yarn from snarling after the Ring frame process. The steamed yarn is kept in a cool environment for 8 hours to retain moisture and stabilize, facilitating the winding process.
Benefits of Wool
Natural and Renewable: Wool is a natural fiber known for its exceptional all-weather protection. Sheep produce a fresh fleece every year, making wool a sustainable and renewable fiber source. Wool growers actively work to enhance efficiency and conserve resources for the future of the wool industry.
Safe: Wool offers natural UV protection, surpassing most synthetic materials and cotton in its effectiveness.
Fire Retardant: Fabrics made entirely of wool are resistant to easy ignition and, if they do catch fire, they burn slowly and self-extinguish when the flame source is removed.
Biodegradable: Natural Merino wool fibers take only a few years to decompose when discarded, enriching the soil for crop cultivation. This is in stark contrast to most synthetic materials, which degrade much more slowly.
Breathable: Wool has an excellent ability to absorb moisture vapor and sweat near the skin, ensuring high breathability.
Durable: A single wool fiber can endure being bent 20,000 times without breaking and will return to its original shape, reducing the need for garment replacement. High-quality wool products maintain their appearance over an extended period.
Easy Care: Woolen fibers have a natural protective layer that resists stain absorption and repels dust due to their static resistance. Recent innovations have made machine washing and tumble drying suitable for many woolen garments.
Multi-climate: Wool actively adapts to changes in body temperature, providing warmth when it’s cold and releasing heat and moisture when it’s hot.
Natural Insulator: Wool effectively insulates homes, retaining warmth and ultimately reducing energy costs.
Elastic: The natural elasticity of wool fibers enables them to stretch with the wearer and return to their original shape, minimizing garment sagging or loss of form.
You may also like:
- Kapok Fiber: Properties, Structure and Production Process.
- What is Linen Fiber? Properties, Structure, and How It Made?
- What is Jute Fiber? Properties, Advantages and Disadvantages.
- What is Hemp Fiber? Properties, Advantages and Disadvantages.
- What is Ramie Fiber? Properties, Advantages and Disadvantages.
- What is Sisal Fiber? Properties, Structure, and How It Made?
- Pina Fiber: History, Properties, Production Process
- Coir Fiber: Properties, Production Process and Advantages
- Silk Fiber: History, Properties, Production Process
- Nylon Fiber: Properties, Advantages and Disadvantages
- Acrylic Fiber: History, Properties, Advantages and Disadvantages
- What is Textile? Definition and Meaning
Share this Article!