Introduction
Kapok fiber comes from the Ceiba tree in tropical rainforests. It’s known for being very lightweight and strong, unlike cotton and wool. When you touch it, it feels soft and cozy, like nature’s silky hug. Kapok fiber also known as Java cotton, Java kapok, ceiba, or silk cotton, comes from Asia and Indonesia. Indonesia is a top exporter of kapok. The kapok trees can grow very tall, up to 55-65 meters, with wide trunks and leaves that look like palms. These trees live for about 55 years and start producing in 4-5 years. In good conditions, each tree can give 330 to 400 fruits a year, leading to 16 kilograms of fiber and 35 kilograms of seeds. On average, you get about 500 kilograms of textile fiber per hectare. Some kapok trees are even more prolific, producing 500 to 4000 fruits in a season, each containing 200 seeds. Surprisingly, each tree makes 1000 to 2,000 pods annually, which are 10–40 cm long and 3–5 cm thick. However, kapok fiber isn’t suitable for spinning because it’s short, lightweight, slippery, brittle, fluffy, and not very elastic, making it challenging to weave effectively. So, it’s mostly used in fabric blends that can be spun, creating softer and more comfortable textiles.
Properties of kapok fiber
Longitudinal and Cross-section: When we inspect kapok fiber closely, we see that it has a smooth, tube-like surface when viewed lengthwise, and from the side, it appears to have a wide, open center. This special hollow structure of kapok fiber is thought to be the reason why it has such a large surface area.
Length and Density: Kapok fibers are 10-35 mm long and are not very dense, measuring around 0.4-0.7 decitex, which is about half as dense as cotton. The reason for this lower density is that kapok has a wide central open space called a lumen.
Color and Luster: Kapok fibers may seem shiny, but they’re fragile and can break easily. They come in colors from yellowish to light brown. Kapok fiber is odorless, fluffy, safe, and won’t cause allergies. It also stays fresh and doesn’t get moldy or decay.
Thermal Insulation: Kapok fibers are excellent at keeping things warm because they’re mostly hollow inside, and they’re even better at insulating than wool.
Water Repellency: Kapok fibers are like nature’s water-resistant shield with their waxy surface, and they’re remarkable at soaking up and holding onto oil, all thanks to the roomy hollow space inside.
Sound Absorption: Kapok fibers can soak up bothersome noises because of their hollow design.
Spinning Quality: The fact that kapok fibers are short, don’t cling well (lack cohesion), and don’t stretch much makes it tough to craft yarns from them by themselves. So, they’re frequently combined with other fibers.
Weaving: Kapok fibers are slippery, making weaving tricky. To solve this, you can treat them with chemicals or plasma to remove the slipperiness. Another way is to weave kapok with other natural fibers like cotton, jute, or flax to make blends.
Dyeing: Kapok fibers repel water and have a waxy coating, which makes dyeing them difficult. That’s why it’s crucial to treat kapok before dying to help it absorb color better.
Antibacterial Property: Kapok fiber has natural antibacterial qualities because it contains plenty of lignin, which acts as a barrier against cellulosic bacteria.
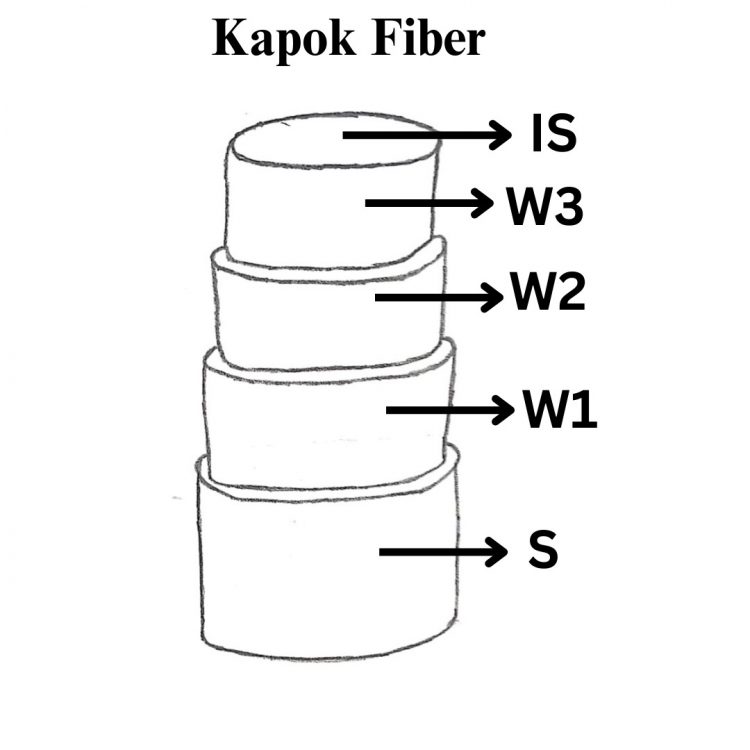
Structure of Kapok fiber
Kapok fibers have a unique cell wall structure that sets them apart from cotton fibers, whether you look at them from the side or end-on. The cell wall consists of five layers: an outer skin (S), a primary wall (W1), a secondary wall (W2), a tertiary wall (W3), and an inner skin (IS). IS, the innermost layer, is thin, measuring 40 to 70 nanometers, and acts as a protective shield for the fiber.W1, the primary wall, is thicker than the outer skin (S) but thinner than both W2 and W3. It’s typically 160 to 240 nanometers thick, with an average of about 200 nanometers. W2, the secondary wall, is around 500 nanometers thick, similar to the tertiary wall (W3). The inner skin (IS) is very thin and uneven, with an average thickness of about 40 nanometers, making it easily visible in cross-sections. Additionally, there are transitional layers (L1 and L2) between W1 and W2, and between W2 and W3.
Composition of kapok fiber
- Composition of kapCellulose: 64%
- Pentose: 23%
- Lignin: 13%
Chemical Composition of kapok fiber
- Cellulose: 35-65%
- Hemi-cellulose: 23%
- Pectin: 23%
- Lignin: 13%
- Extractives: 0%
- Moisture: 0%
Physical parameters of kapok fiber
- Fineness Denier: 0.4-0.7
- Tenacity g/den: 1.4-1.74
- Elongation at break: 1.8-4.23
- Fiber color range: Shades ranging from ivory white to camel brown.
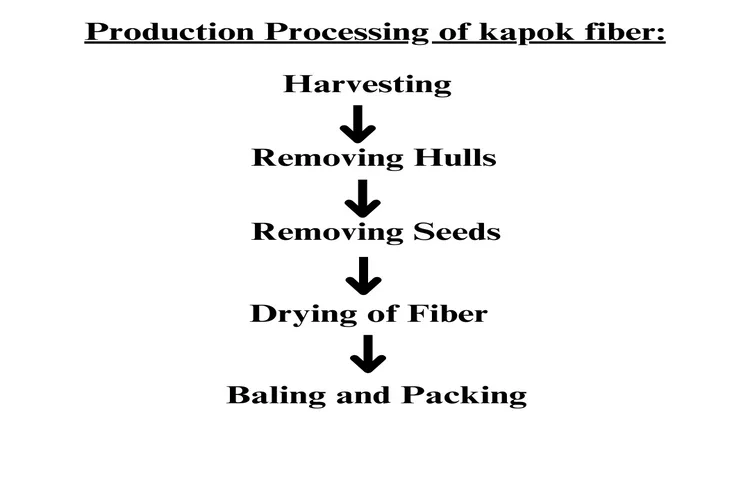
Production Processing of kapok fiber
- Harvesting: Kapok is picked when the fruits are fully ripe. Pods are collected as they fall naturally to the ground or by cutting them from the tree. Hand-harvesting is used for open seedpods, and bamboo sticks are employed to crack the tough husks of closed seedpods, releasing the fibers. When ripe, seedpods split open, releasing the compressed textile fibers.
- Removing Hulls: To get rid of the hulls, ripe fruits are dried in the sunlight. The fibers and seeds are then separated manually from the pods.
- Removing Seeds: Seeds are separated from the fibers by stirring the mixture in baskets or sieve-like devices resembling drums. This causes the seeds, along with any pod debris or dry leaves, to settle at the bottom of the container, making them easy to collect.
- Drying of Fiber: Kapok fibers are sun-dried for three to five hours.
- Baling and Packing: The dried kapok fibers are compressed into bales for packaging.
You may also like:
- Explore The Different Types Of Textile Fibers
- Structure and Properties of Cotton Fiber
- What is Linen Fiber? Properties, Structure, and How It Made?
- What is Jute Fiber? Properties, Advantages and Disadvantages.
- What is Hemp Fiber? Properties, Advantages and Disadvantages.
- What is Ramie Fiber? Properties, Advantages and Disadvantages.
- What is Sisal Fiber? Properties, Structure, and How It Made?
Share this Article!