Introduction
Leaving out silk, most tech-related natural fibers are collected as staple fibers with distinct lengths. During the spinning or yarn manufacturing process, the fibers entwine to boost friction, creating a staple fiber yarn. Yarns are the foundation of fabric creation. Their thickness spans a wide range and is usually measured in yarn count. It is a number that signifies the yarn’s fineness or coarseness. Various methods, like ring spinning or air-jet spinning, add the needed twists to the yarn, and the chosen spinning technology affects the yarn’s properties.
Machine Flow Chart for the Manufacturing Process of Cotton Yarn
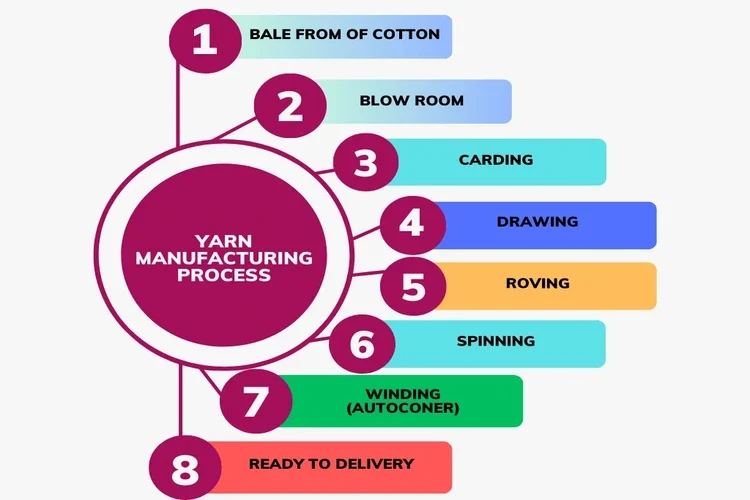
Bale from of cotton
In the bundles of raw cotton, there are always impurities known as ‘Trash.’ This includes broken seeds, husks, broken leaves, dirt, and short fibers. The amount of trash can vary from 1% to 15%, depending on the quality of the fibers. Usually, imported cotton fibers are in a tightly compressed bale form for ease of handling.
Blow Room
During the spinning process, the first step involves the cleaning and opening of cotton using beaters and openers. This step in the yarn manufacturing process aids in removing foreign materials such as dust particles, cotton seeds, and other impurities. The cleaning and opening of cotton tufts result in the formation of a cotton lap.
Carding
Carding stands at the heart of the yarn manufacturing process, where we eliminate minute impurities like small seed particles and immature fibers. This step involves straightening and aligning the fibers. In the carding process, the Blow room lap is transformed into the card sliver.
Drawing
In the drafting process, fibers align side by side. Up to eight carded slivers are placed into the Draw Frame, where they experience stretching and straightening, resulting in the creation of a single sliver. Moreover, the blending of fibers can be performed at this stage.
Roving
In this step, we continue drafting to align the fibers. The sliver from the Draw Frame is too thick to go directly into the Ring Frame, so we stretch and make it thinner through drafting and a bit of twisting to fortify the roving. The end result from the Simplex is known as roving.
Spinning
The roving enters the Ring Frame, transforming into yarn through additional drafting and twisting. We make adjustments to the drafting and twisting to achieve the desired thickness for the yarn.
Winding
Winding makes big yarn packages that are easy to unwind. It helps use yarn efficiently on other machines, saving money. All yarns made on the ring frame are wound into large cones using the Autocone winding machine. This machine also fixes any yarn issues with the help of a yarn clearer.
You may also like:
- Count of Yarn: Explanation and Varieties
- Identification of Textile Fibers
- What is Hemp Fiber? Properties, Advantages and Disadvantages.
- What is Ramie Fiber? Properties, Advantages and Disadvantages.
- What is Sisal Fiber? Properties, Structure, and How It Made?
- Pina Fiber: History, Properties, Production Process
- Coir Fiber: Properties, Production Process and Advantages
- Rayon Fiber: History, Properties, Advantages and Disadvantages
- Acrylic Fiber: History, Properties, Advantages and Disadvantages
- Nylon Fiber: Properties, Advantages and Disadvantages
Share this Article!