Weaving On A Handloom
Weaving is one of the oldest ways people have made fabric, where two strands of yarn or thread cross over each other at right angles to form cloth. The simple tool that brings this process to life is the loom. The loom is the heart of hand weaving, and depending on how it’s built and used, there are many different kinds of handlooms and even semi-automatic looms that follow the same tradition. Hand-weaving is a careful, hands-on craft where the loom, whether it stands tall or lies flat, moves under the guidance of skilled hands, with no help from electricity or other power. The long threads running lengthwise are called the “warp,” and the threads crossing over them are the “weft.” The warp makes the face of the fabric, while the weft forms its base or backing.
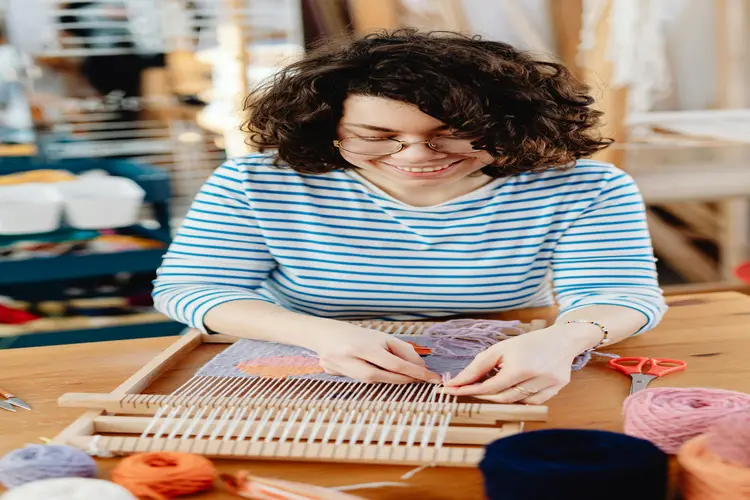
The Process of Handloom Weaving
The journey of handloom weaving starts with growing cotton or silk. Once the fibers are ready, they’re harvested and prepared for spinning. Using a simple spinning wheel, skilled hands carefully turn the raw cotton or silk into thread—a process that takes both patience and mastery.
After the thread is spun, it’s dyed and wound onto small wooden spools called pirns. These are placed on the handloom, an age-old tool powered by the weaver’s hands and feet. With the loom, the weaver guides the warp and weft threads, crafting patterns and designs with each careful movement of the pedals and levers.
Handloom weaving is more than a craft—it’s a labor of time and dedication. A single saree or pavadai set can take days or even weeks to finish, depending on the design and the weaver’s skill.
The process also includes steps like sizing, thread reeding, and pin winding, all of which come together to form the final fabric.
Sizing is the process of applying a starch-based adhesive to the thread before it’s wound onto pirns for weaving. This coating stiffens the thread, making it stronger and easier to manage during the weaving process.
Thread reeding, or slaying, is where the threads are carefully arranged in the correct order on the loom, setting the stage for the weaving to begin.
Pirn winding involves wrapping the prepared thread onto wooden spools called pirns, which hold the thread ready for weaving.
Handloom weaving is a time-honored craft steeped in tradition, transforming raw cotton or silk into thread and then weaving it into fabric. It demands a high level of skill, patience, and a keen eye for detail. Steps like sizing, thread reeding, and pirn winding are essential for achieving a quality and durable final product.
More than just a craft, handloom weaving links us to our heritage, preserving the cultural practices of those who came before us and honoring the artistry that has been passed down through generations.
You may also like:
- Count of Yarn: Explanation and Varieties
- Yarn Manufacturing Process
- What is Ramie Fiber? Properties, Advantages and Disadvantages.
- What is Sisal Fiber? Properties, Structure, and How It Made?
- Pina Fiber: History, Properties, Production Process
- Coir Fiber: Properties, Production Process and Advantages
- Rayon Fiber: History, Properties, Advantages and Disadvantages
- Acrylic Fiber: History, Properties, Advantages and Disadvantages
- Nylon Fiber: Properties, Advantages and Disadvantages
Share this Article!